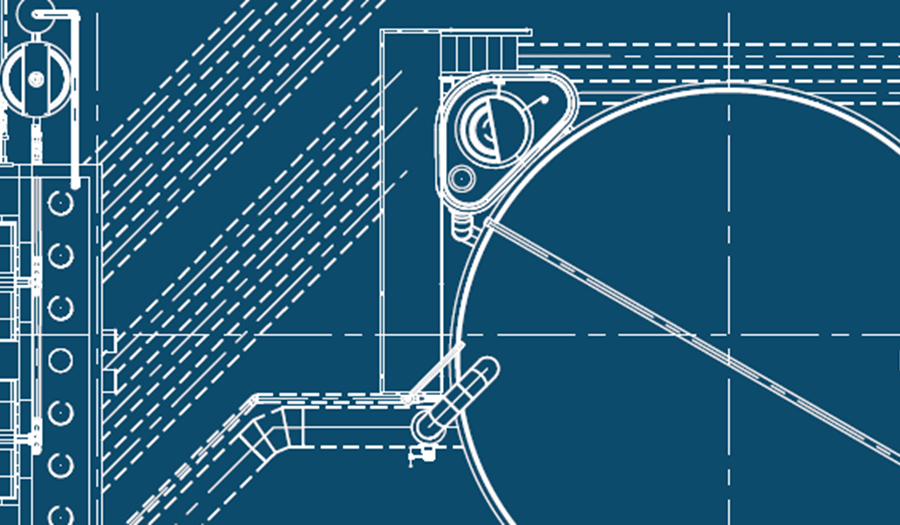
What’s Holding Back RAS?
3/14/2024
PR Aqua has been a knowledge leader in the aquaculture industry since 1985. Starting out in the design and construction of fiberglass tanks for the blossoming salmon farming industry in British Columbia, Canada, we advanced to the development of our own line of microscreen drum filters, fish handling products, and gas balancing equipment. In 1996, we started an engineering division of the company to provide greater value to our customers by packaging our equipment together into efficient and integrated systems. Two years later, this culminated in the design and construction of western Canada’s first Recirculating Aquaculture System (RAS) project that is still in operation today. Similarly, we designed and built one of Canada’s first land-based RAS salmon grow-out system to raise Atlantic salmon to harvest size. The Kuterra Salmon farm was constructed in 2013 and continues to operate producing harvest sized fish which are sold to restaurants and markets throughout British Columbia.
First RAS in Western Canada – Target Marine circa 1998
Over the years, PR Aqua has remained at the forefront of the industry by being continuing to be a company of firsts: first partial recirculating aquaculture system (PRAS) in Columbian River basin; first and largest public RAS & PRAS, both in scale and dollar value in the United States; and first commercial RAS in Chile.
State of Alaska – William Jack Hernandez Hatchery, Anchorage, AK
For over 25 years, PR Aqua has been providing our customers with engineered RAS solutions to suit their specific fish production and water quality needs. We continue to work with our customers, many of whom are repeat clients, and some of which are the largest salmon farming companies in the world, to develop innovative systems to grow high quality fish in facilities that are well thought out, are energy efficient, and easy to operate.
As the aquaculture industry evolves, there is a greater interest to start growing fish to harvest size in land-based systems. These projects are complex to design and expensive to build, but the rewards of being able to locate them almost anywhere, such as large urban markets, are sure to pay off in the long term. However, building such a facility is not for the inexperienced, requires extensive investment, and sometimes years of permitting and detailed design before a shovel is even put into the ground. It is for this reason that collaboration with a knowledgeable and experienced design consultant is of utmost importance. Without appropriate guidance, solutions produced can be inappropriate, too costly, or don’t adequately optimize the production goals.
Getting a RAS project constructed has become increasingly difficult over the past 24 months. The high cost of borrowing and recent project failures are just some of the factors preventing investors from committing their resources. Over the coming months, PR Aqua will be presenting our thoughts on the obstacles facing RAS and how we have developed solutions to help mitigate some of the inherent challenges.
PR Aqua is working to develop standardized “modular” production units that will make RAS more investable by providing increased certainty of costs, both in CAPEX and OPEX. These modular systems will reduce development and construction timelines, and be designed to mitigate risk. Optimization of CAPEX-to-production ratios to determine the highest efficiency possible and define optimal production outputs is a key feature of these designs and will be presented in detail.
Modular RAS for Grow-out
Stay tuned for our next article where we will explore how our experience has shown us the importance of bioplanning as a key part of the early design phase and how decisions made when bioplanning can have dramatic effects on the budget and scale of a facility.
For more information about PR Aqua, please visit our website at www.praqua.com or contact us at info@praqua.com